Welcome to hongqing!
Service hotline:0769-83342081 Email:sales@dghongqing.com
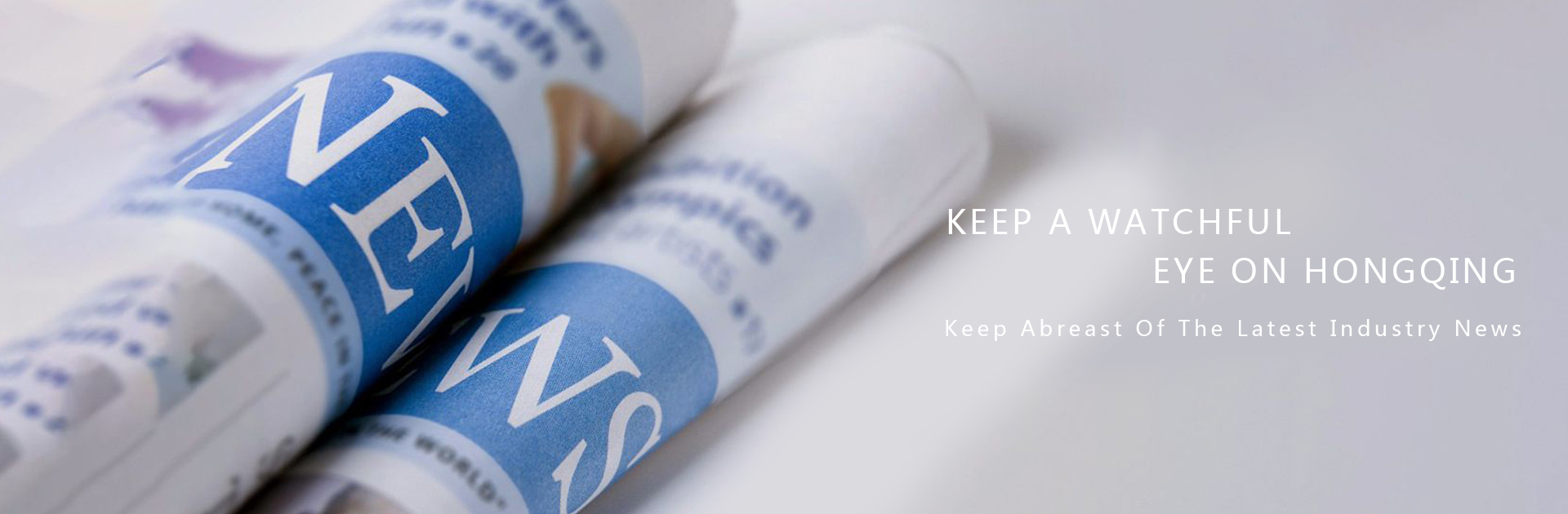
01 shoot tip
The glue usually flows from the nozzle into the injector, but in some molds, the nozzle is part of the mold because it extends to the bottom of the mold. There are two main types of muzzle: open muzzle and closed muzzle. In injection molding production, open injectors should be used more, because they are cheaper and have less possibility of retention.
If the injection molding machine is equipped with a pressure removal device, then even the lower viscosity glue can be used this nozzle. Sometimes it is necessary to use a closed nozzle, which ACTS as a stop-flow valve and blocks the plastic shade in the cylinder. Make sure the nozzle is properly inserted into the nozzle sleeve and the top hole is slightly smaller than the nozzle sleeve so that the nozzle can be withdrawn from the mold more easily. The hole of the nozzle sleeve should be 1mm larger than that of the shooting nozzle, that is, the radius of the shooting nozzle should be 0.5mm smaller than that of the shooting nozzle sleeve.
02 filter and combined nozzle
Plastic impurities can be removed by a filter in the ductile nozzle, whereby the melt and plastic flow through a channel separated by inserts into a narrow space. These narrow and interstitial Spaces remove impurities and improve the mixing of plastics. Thus, by extension, a solid mixer can be used for better mixing. These devices can be installed between the injection cylinder and the nozzle for the separation and remixing of the melt, mostly to channel the melt through the stainless steel.
03 exhaust
Some plastics in injection need to be in the injection cylinder exhaust, let the gas out. Most of the time the gas is just air, but it can be water or a monomolecular gas released from the melt. If this gas cannot be released, it is compressed by the melt and brought to the mold, where it expands and bubbles form in the product. To drain the gas before it reaches the nozzle or die, reduce or reduce the screw root diameter to reduce the pressure of the glue in the injection cylinder.
Here, gas can be discharged through holes or holes in the injection cylinder. Then the root diameter of the screw was increased and the volatile melt adhesive was applied to the nozzle. The injection molding machine equipped with this facility is called an exhaust injection molding machine. The exhaust injection molding machine should have a catalytic burner and a good smoke extractor to remove potentially harmful gases.
Increase the effect of back pressure
To obtain a high quality melt, the plastic is heated or melted consistently and mixed well. Only by using the right screw can the mixture be melted and mixed properly and with enough pressure (or back pressure) in the injection cylinder to obtain the consistency of mixing and heat.
Increase the resistance of the return oil can generate back pressure in the firing cylinder. But the screw takes longer to reposition, so there is more wear and tear in the injection molding machine drive system. As far as possible to maintain back pressure, isolated from the air, also need to melt temperature and mixing range of the same
05 check valve
Either screw is usually fitted with a stop valve at the tip and a decompression (rewind) device or special nozzle may be fitted to prevent plastic from escaping from the nozzle. If used to prevent miscarriage, it must be checked regularly as it is an important part of the firing cylinder. At present, the switch nozzle is not commonly used, because the gun nozzle equipment is prone to leakage of plastic and decomposition. At present, each type of plastic has a specific type of nozzle.
Screw back (retainer)
Many injection molding machines are equipped with a screw back or suction device. When the screw is stopped, it is hydraulically withdrawn to suck back the plastic tip of the nozzle. The device permits the use of an open nozzle. The amount of recirculation may be reduced because entering the air can cause problems for some plastics.
07 screw pad
Most of the injection cycle is required to adjust the spin of the screw, so that when the screw injection is finished, most of them will have a small amount of cushion plastic, which can ensure the screw to achieve effective propulsion time and maintain a fixed firing pressure. The padding material of the small-sized injection molding machine is about 3mm; The large injection molding machine is 9mm. No matter how large the screw pad is used, it must be kept constant. Now the size of screw pad can be controlled within 0.11mm.
Rotation speed of 08 screw
The rotational speed of the screw has a significant effect on the stability of the injection molding process and the heat applied to the plastic. The faster the screw rotates, the higher the temperature. When the screw rotates at a high speed, the friction (shear) energy transmitted to the plastic increases the plasticization efficiency, but also increases the inhomogeneity of melt temperature. Because of the importance of screw surface speed, the screw rotation speed of large injection molding machine should be less than that of small injection molding machine, because the shear heat energy generated by large screw is much higher than that of small screw at the same rotation speed. The speed at which the screw rotates varies depending on the plastic.